Private Water Wells
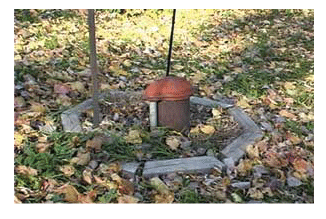
To keep your well safe, you must be sure that possible sources of contamination are not close by. Experts suggest the following distances as a minimum for protection — farther is better :
- septic tanks: 50 feet;
- livestock yards, silos, septic leach fields: 50 feet;
- petroleum tanks, liquid-tight manure storage and fertilizer storage and handling: 100 feet; and
- manure stacks: 250 feet.
Many homeowners tend to forget the value of good maintenance until problems reach crisis-levels. That can be expensive. It’s better to maintain your well, find problems early, and correct them to protect your well’s performance. Keep up-to-date records of well installation and repairs, plus pumping and water tests. Such records can help spot changes and possible problems with your water system. If you have problems, ask a local expert to check your well construction and maintenance records. He or she can see if your system is okay or needs work.
Protect your own well area. Be careful about storage and disposal of household and lawn-care chemicals and wastes. Good farmers and gardeners minimize the use of fertilizers and pesticides. Take steps to reduce erosion and prevent surface water runoff. Regularly check underground storage tanks that hold home heating oil, diesel, or gasoline. Make sure your well is protected from the wastes of livestock, pets and wildlife.
outside of the casing, or through the casing and into the well.
Dug Well Construction Features
- The well should be cased with a watertight material (for example, tongue-and-groove pre-cast concrete), and a cement grout or bentonite clay sealant poured along the outside of the casing to the top of the well.
- The well should be covered by a concrete curb and cap that stands about a foot above the ground.
- The land surface around the well should be mounded so that surface water runs away from the well and is not allowed to pond around the outside of the wellhead.
- Ideally, the pump for your well should be inside your home or in a separate pump house, rather than in a pit next to the well.
Land activities around a dug well can also contaminate it. While dug wells have been used as a household water supply source for many years, most are relics of older homes, dug before drilling equipment was readily available, or when drilling was considered too expensive. If you have a dug well on your property and are using it for drinking water, check to make sure it is properly covered and sealed. Another problem relating to the shallowness of a dug well is that it may go dry during a drought when the ground water table drops.
Like dug wells, driven wells pull water from the water-saturated zone above the bedrock. Driven wells can be deeper than dug wells. They are typically 30 to 50 feet deep and are usually located in areas with thick sand and gravel deposits where the ground water table is within 15 feet of the ground’s surface. In the proper geologic setting, driven wells can be easy and relatively inexpensive to install. Although deeper than dug wells, driven wells are still relatively shallow and have a moderate-to-high risk of contamination from nearby land activities.
Driven Well Construction Features
- Assembled lengths of 2- to 3-inch diameter metal pipes are driven into the ground. A screened “well point” located at the end of the pipe helps drive the pipe through the sand and gravel. The screen allows water to enter the well and filters out sediment.
- The pump for the well is in one of two places: on top of the well, or in the house. An access pit is usually dug around the well down to the frost line, and a water discharge pipe to the house is joined to the well pipe with a fitting.
- The well and pit are capped with the same kind of large-diameter concrete tile used for a dug well. The access pit may be cased with pre-cast concrete.
To minimize this risk, the well cover should be a tight-fitting concrete curb and cap with no cracks, and should sit about a foot above the ground. Slope the ground away from the well so that surface water will not pond around the well. If there’s a pit above the well, either to hold the pump or to access the fitting, you may also be able to pour a grout sealant along the outside of the well pipe. Protecting the water quality requires that you maintain proper well construction and monitor your activities around the well. It is also important to follow the same land-use precautions around the driven well as described under dug wells.
Drilled wells penetrate about 100 to 400 feet into the bedrock. Where you find bedrock at the surface, it is commonly called ledge. To serve as a water supply, a drilled well must intersect bedrock fractures containing ground water.
- The casing is usually metal or plastic pipe, 6 inches in diameter, that extends into the bedrock to prevent shallow ground water from entering the well. By law, the casing has to extend at least 18 feet into the ground, with at least 5 feet extending into the bedrock. The casing should also extend a foot or two above the ground’s surface. A sealant, such as cement grout or bentonite clay, should be poured along the outside of the casing to the top of the well. The well should be capped to prevent surface water from entering the well.
- Submersible pumps, located near the bottom of the well, are most commonly used in drilled wells. Wells with a shallow water table may feature a jet pump located inside the home. Pumps require special wiring and electrical service. Well pumps should be installed and serviced by a qualified professional registered with your state.
- Most modern drilled wells incorporate a pitless adapter designed to provide a sanitary seal at the point where the discharge water line leaves the well to enter your home. The device attaches directly to the casing below the frost line, and provides a watertight sub-surface connection, protecting the well from frost and contamination.
- Older drilled wells may lack some of these sanitary features. The well pipe used was often 8, 10 or 12 inches in diameter, and covered with a concrete well cap either at or below the ground’s surface. This outmoded type of construction does not provide the same degree of protection from surface contamination. Also, older wells may not have a pitless adapter to provide a seal at the point of discharge from the well.
Hydrofracting a Drilled Well
Hydrofracting is a process that applies water or air under pressure into your well to open up existing fractures near your well, and can even create new ones. Often, this can increase the yield of your well. This process can be applied to new wells with insufficient yield and to improve the quantity of older wells.
How can I test the quality of my private drinking water supply?
The first step to protect your health and the health of your family is learning about what may pollute your source of drinking water. Potential contamination may occur naturally, or as a result of human activity.
What are some naturally occurring sources of pollution?
What human activities can pollute ground water?
|
Private, individual wells are the responsibility of the homeowner. To help protect your well, here are some steps you can take:
Have your water tested periodically. It is recommended that water be tested every year for total coliform bacteria, nitrates, total dissolved solids, and pH levels. If you suspect other contaminants, test for those. Always use a state-certified laboratory that conducts drinking water tests. Since these can be expensive, spend some time identifying potential problems. Consult your InterNACHI inspector for information about how to go about water testing.
Identify potential problems as the first step to safe-guarding your drinking water. The best way to start is to consult a local expert — someone who knows your area, such as the local health department, agricultural extension agent, a nearby public water system, or a geologist at a local university. Be aware of your surroundings. As you drive around your community, take note of new construction. Check the local newspaper for articles about new construction in your area. Check the paper or call your local planning and zoning commission for announcements about hearings or zoning appeals on development or industrial projects that could possibly affect your water. Attend these hearings, ask questions about how your water source is being protected, and don’t be satisfied with general answers. Ask questions, such as: “If you build this landfill, what will you do to ensure that my water will be protected?” See how quickly they answer and provide specifics about what plans have been made to specifically address that issue. Identify Potential Problem SourcesTo start your search for potential problems, begin close to home. Do a survey around your well to discover:
If any of these items apply, it may be best to have your water tested and talk to your local public health department or agricultural extension agent to find ways to change some of the practices which can affect your private well. |
Common Sources of Ground Water Contamination
Category | Contaminant Source |
Agricultural |
|
Commercial |
|
Industrial |
|
Residential |
|
Other |
|
Leave a Reply
Want to join the discussion?Feel free to contribute!